炼钢过程中各类铁合金的加入顺序.docx
《炼钢过程中各类铁合金的加入顺序.docx》由会员分享,可在线阅读,更多相关《炼钢过程中各类铁合金的加入顺序.docx(5页珍藏版)》请在第壹文秘上搜索。
1、炼钢过程中各类铁合金的加入顺序铁合金的加入顺序是首先加入脱氧能力弱的,然后加入脱氧能力较强的。一股在扒渣结束以后,增碳操作完成,加入部分渣料造还原渣以后开始加入合金。不同合金的加入要求分别如下:(1)硅铁在冶炼硅钢或弹簧钢及耐热钢时,需加入大量硅铁进行合金化、所加入的硅铁必须长时间烤红。主要原因是硅铁中含有较多的氢气,烤红后可去除,而且预热硅铁也可加速熔化;此外,由于硅铁较轻,大量加入炉内时,必然有一部分硅与炉渣起脱氧作用,生成酸性产物二氧化硅,降低了局部炉渣的碱度,这样对钢的质量是不利的。为了防止这种情况的产生,在加硅铁的前后要加入适量的石灰,以保持炉渣碱度,并用大电压送电几分钟,使炉渣熔化
2、和反应良好,成为均匀的臼渣。硅铁的回收率在90%-98%之间。在精炼中,当化学成分调整好后,温度适当,渣子良好,这时就可以加入硅铁。加入以后在10-25min之内出钢。如果时间太短,硅铁来不及完全熔化,而且硅在钢内分布也不均匀。如时间太长,容易使钢液吸收气体,影响钢的质量。(2)隹铁钵铁在造还原渣的同时就可以加入,钵一般第一次控制在成分的下限。镒铁的回收率在95%以上。(3)铜冶炼耐候钢时,铜在钢中能提高钢的淬透性和耐腐蚀性能,钢中的铜不易氧化,故可在装料时或氧化期加入,回收率也稳定在95%以上。由于铜较贵,一般最好将含铜生铁、含铜的废钢铁料或含铜铁矿在熔化期配加一部分,少量的铜在还原期调整,
3、以尽量减少纯铜的用量。(4)格铁辂铁一般在还原期初期加入。格与氧的亲和力比铁与氧的亲和力大,也就是格比铁容易氧化。如果在熔化期、氧化期加入,珞会被靠化,不仅造成合金元素的损失,而且使炉渣变稠,影响去磷和冶炼操作,所以铭铁要在还原期加入。加入后如渣子变成绿色,说明渣子脱氧不良,必须加强还原,把渣中的氧化辂还原。还原良好后,渣子会变成臼色。铭铁的IU1.收率在还原期向渣条件下大于95%o(5)钮铁锐铁要在还原期加入。锐和轨的亲和力很大,很易氧化,故不能在氧化期加入,只能在还原期炉渣和钢液脱氧良好后加入。由于锐铁加入使钢水极易吸收空气中的氮气,影响钢的质量,因此不能过早加入,只能在出钢前加入。但是帆
4、铁熔化需要一定时间,所以应在出钢前10-35min加入,加入量较少时,时间控制在下限,加入量较大时控制在中上限。钢铁的回收率和硅铁的回收率接近。(6)铝铁拓铁是一个难熔的合金,一般在还原期初期加入,这样可以保证熔化完全,成分均匀。如果在后期加入,离出钢没有几分钟,钥铁来不及完全熔化,可能造成在钢液中分布不均匀,造成冶炼时间增加。铝铁的回收率一般大于98%o(7)锯铁银是一种与氧的亲和力较弱的元素,所以在治炼过程中比较容易控制和掌握。一般在还原期的初期加入,加入20min以后才能够出钢,以促使其熔化均匀。当采用不氧化法冶炼时,锂也可在装料时加入,银的回收率一般大于95%。(8)筲铁鸨铁的特点是密
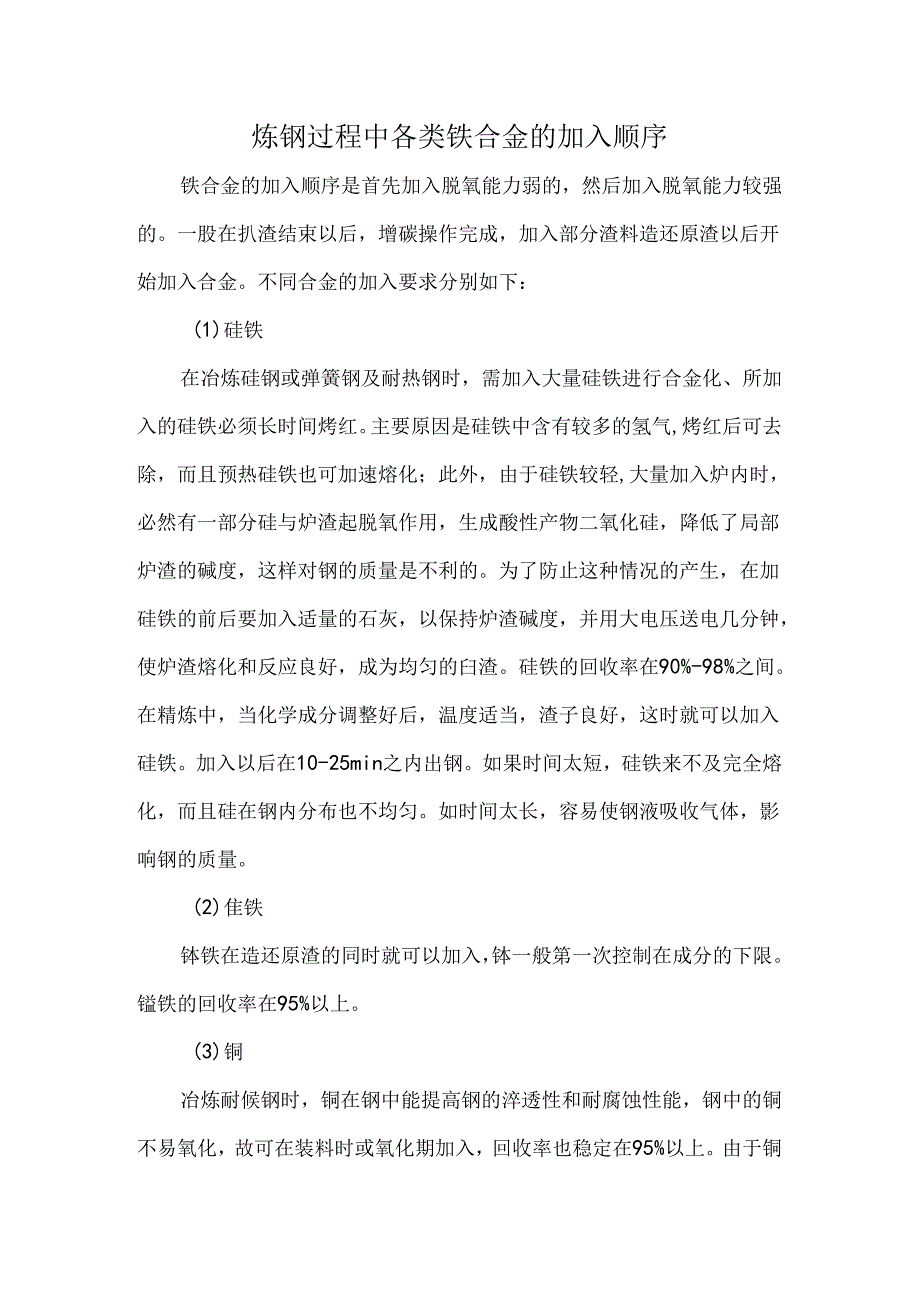
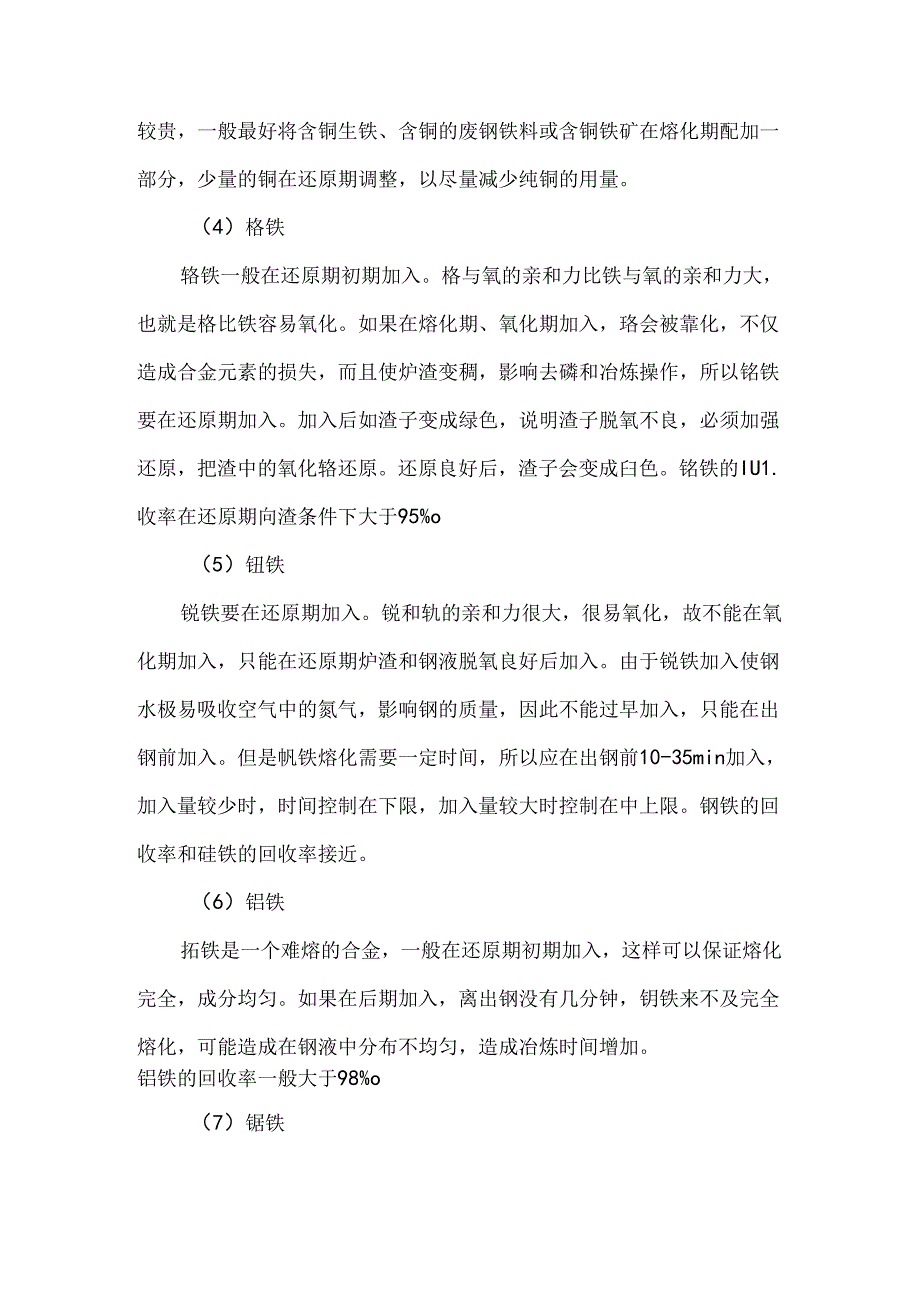
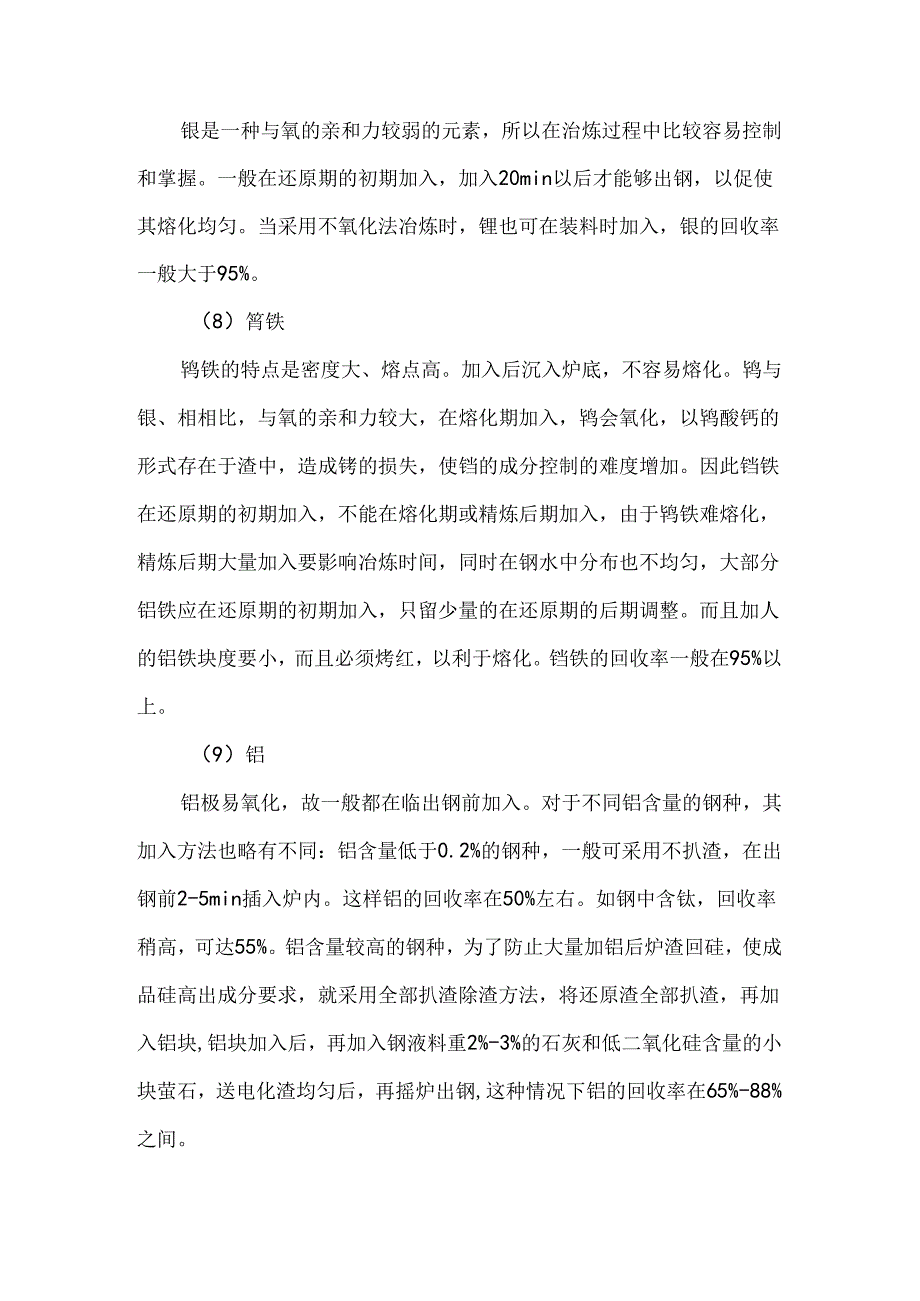
- 配套讲稿:
如PPT文件的首页显示word图标,表示该PPT已包含配套word讲稿。双击word图标可打开word文档。
- 特殊限制:
部分文档作品中含有的国旗、国徽等图片,仅作为作品整体效果示例展示,禁止商用。设计者仅对作品中独创性部分享有著作权。
- 关 键 词:
- 炼钢 过程 各类 铁合金 加入 顺序
