2500t d回转窑托轮轴瓦事故的处理及实例分析.docx
《2500t d回转窑托轮轴瓦事故的处理及实例分析.docx》由会员分享,可在线阅读,更多相关《2500t d回转窑托轮轴瓦事故的处理及实例分析.docx(9页珍藏版)》请在第壹文秘上搜索。
1、1事故概述我公司二线4m60m回转窑,三档支撑,单传动,单液压挡轮,斜度3.5%,主减速器型号ZSY63O-35.5-V,速比34.601,主电动机型号ZSN4-355-092,功率315kW,其窑体旋向从窑头往窑尾看为逆时针方向。其主要结构及各档轴承座布置见图1,该生产线自2006年9月投产运行至今,设计产量为2500t/d。2#4#2#4#2#4#图1回转窑结构及各档轴承座布置示意各档关键组件的轮带分别被两组托轮呈60。夹角支撑传递动力。各托轮轴承座内结构见图2,由托轮轴、球面瓦、衬瓦、止推圈及油勺、油勺支架等组成。12月28日17点40分,中控操作员在正常操作时发现窑主传电流从350A升
2、至600A,且维持了几秒。针对此异常电流情况,中控操作马上电话通知岗位现场排查,但由于岗位人员未认识到问题的严重性,只对现场相关设备作了简单的检查后,以“一切正常”反馈给了中控,继续维持运行,但时隔5h13min(即当天的22点53分),窑电流又冲到100OA以上,随即第11档3#轴承座温度由50C陡升至75且失去控制,中控被迫止料停窑,再次通知岗位排查,检查后发现H档1#轴承座内托轮轴肩靠尾端沿止推圈卡槽处整体断裂,如图3所示,而同轴的另一端即3#轴承座密封及油勺被刮坏,3#托轮轴瓦已严重缺油冒烟,用测温仪现场测试轴面温度己达80C,且还在上涨,轴上已有明显铜屑,从而导致了此次恶性事故的发生
3、。图2回转窑各档托轮轴端结构放大示意断裂线断裂线图311档1#托轮轴头断裂示意2抢修措施我公司及时组织相关人员进行抢修:其一通知维修轴瓦技术娴熟、作风过硬的维修队伍进场;其二对整个检修现场所需工器具、吊装设备从安全角度上作全面的风险评估检查,对施工现场的安全范围半径、临时安全照明、施工的安全监管等进行了详细的现场交底;其三,对此次抢修的关键配件及施工技术的相关要求进行落实:由于公司此档托轮及轴均无配件,故整体安排是将1#轴承座内断裂的轴头作焊接加固处理,对3#轴与轴瓦配合面由于烧瓦造成的铜屑、毛刺等做手工打磨处理,对配件库已落实好的同型号规格的新轴(铜)瓦做重新研刮、修配的重点处理,其他相关组
4、件只作例行检查处理;其四,考虑当时市场需求及窑内温度较高而无法深入内部系统排查,故在原因未彻底分析清楚之前,暂只恢复到前期正常投料量的90%先行组织生产。3具体抢修施工要点先将顶窑及维修用的相关工器具运至现场。顶窑前,为释放窑体偏心力,手动松开辅传抱闸,然后在II挡轮带中心位架设固定40Ot液压油顶及顶窑专用弧板,将II挡轮带顶起约20mm,为安全起见,采用保险垫铁将千斤顶两边塞牢。然后,拆卸1#、3#组托轮两边的轴承座隔热板、冷却水管、石墨板支架、测温装置等相关组件,同时放尽1#、3#轴承座内润滑油,并拆除两边轴承座端盖、轴承座内淋油盘、油勺等相关组件,利用50t吊车及钢丝绳将1#、3#轴承
5、座上盖、托轮及轴吊至窑墩地面,这样空旷的场地,为后续的施工安全及进度创造了非常有利的条件。为尽可能争取时间,通过不断优化现场施工方案后,决定1#、3#两轴承底座可不做移动,但各轴承底座内的球面瓦及1#端托轮瓦等必须注意例行的技术检测及油泥的清理。对于3#托轮轴由于烧瓦时产生的表面磨痕的修复,先用细铿刀修刮、再用油石反复打磨,直至整个轴面光滑、无高点方可。3#托轮新轴瓦的换新是本次抢修时间和技术的关键节点,其主要技术指标必须符合:托轮轴瓦背与球面瓦刮研配合,其接触角为90。,接触面为每2.5cm2.5cm上的接触斑点不得少于23点;托轮瓦面与轴颈的接触角度为30,接触面接触斑点不少于12点/cm
6、2;轴瓦面与轴颈的侧间隙为0.0010.0015D(D为轴的直径),且用涂色法检查各配合表面,着色均匀、接触良好,而轴瓦进、出口侧游隙应做两次各分五处用塞尺进行测量,即第一次放在轴颈上测量;第二次在组装受力时测量,并做好相关检测记录,作业时轻吊轻放,避免轴瓦受损。最后,待新瓦修刮全面达到技术要求,各相关配件全部清洗干净后,将球面瓦及衬瓦吊至轴承座内,并用50t吊车及手动葫芦将托轮及轴吊至1#、3#轴承座内,在轴瓦面上抹上润滑油并用白布覆盖,落下时要防止托轮及轴的滚动,并控制其轴向窜动。而1#开裂轴头的修复,则先用手砂轮机将裂纹口毛刺清除干净、再磨削裂纹口呈30。坡口,焊工用手工电弧及25mm2
7、5mm长度低于轴头直径470mm的钢板作加强焊接处理。经过维修人员连续奋战18h后,窑顺利投产。4原因分析针对此次突发事故,通过上述的重点安排及抢修,运行32d后,到了次年的年修阶段,于是公司再次组织相关技术人员深入窑内,通过全方位排查、分析及相关处理,同时结合前后期的生产运行情况,特别是年修开机后稳定而连续的运行,也终于找到了这次事故的原因,其具体可初步描述为:窑提产,窑内填充率增加,窑体窜动加剧,但由于窑尾筒体与烟室间隙不均引发剧烈碰撞,碰撞所产生的作用力迅速传递于各组托轮上,而间隙最小的H档1#托轮止推圈形成反作用力致使该事故轴止推圈瞬间崩裂,同时伴随窑电流飙升、同轴的另一端油勺破坏、轴
8、瓦被烧的一系列后果。4.1 提产和事故的关联性回转窑筒体与水平呈一定的斜度安装在托轮上,经过长期的运行后,由于基础的变化、筒体的弯曲度、各托轮与轮带表面的不均匀磨损、接触表面摩擦系数的变化等,窑体运转时一般均存在一定幅度的窜动。经分析,事故前两天,分厂工艺根据整个窑况及产质量情况,结合其他国内同类窑型的投料量情况(一般均为熟料日产3000t左右),制定了尝试提产的计划,生料投料从175t/h逐渐提高至186th,且要求每3h增加0.5t量控制,生产第一天后,各相关设备运行未见明显异常,但随着后续的生产,窑内填充率在慢慢增加,导致整个窑体窜动的幅度增加,同时托轮受力也发生了一定的变化,只是未引起
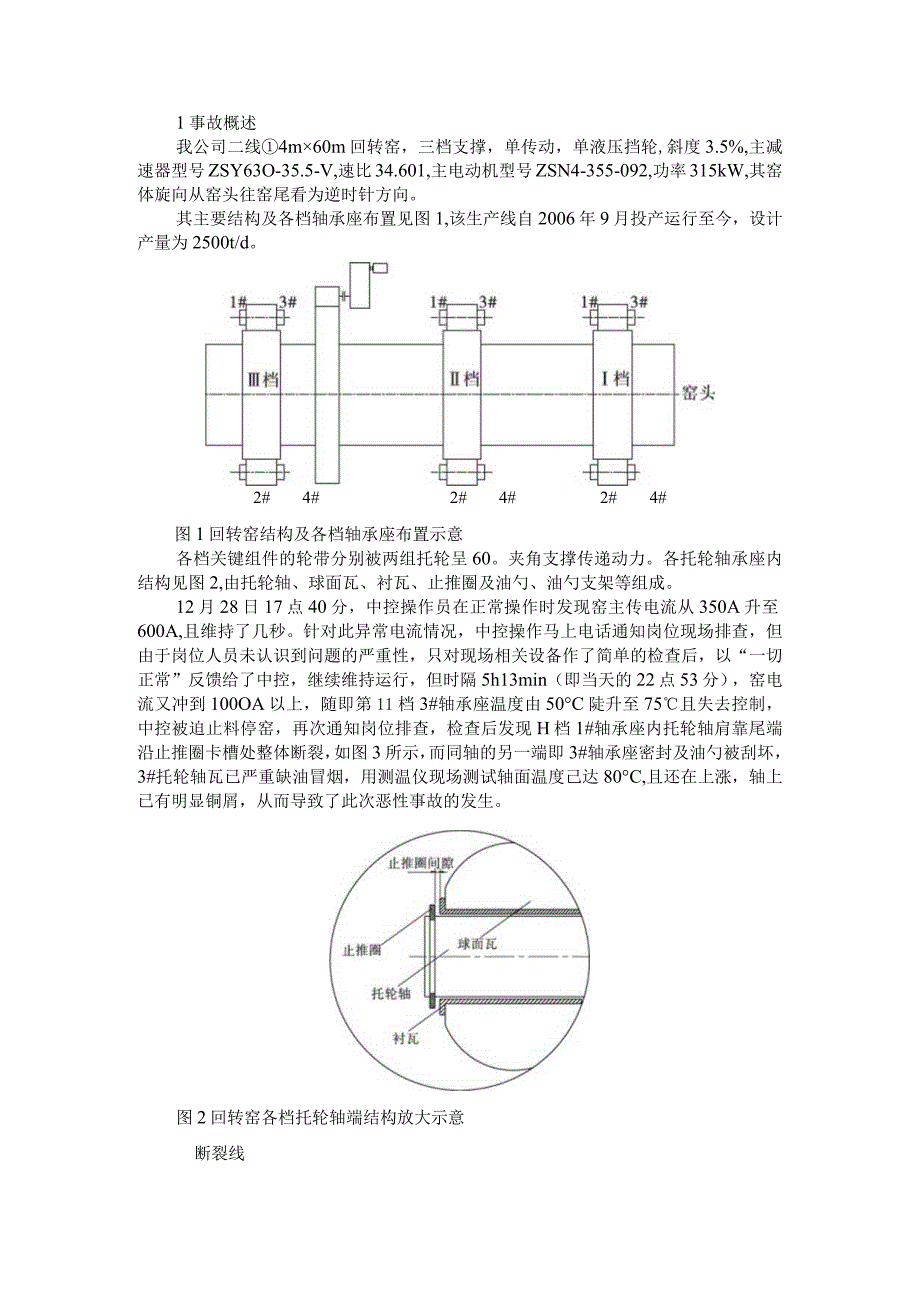
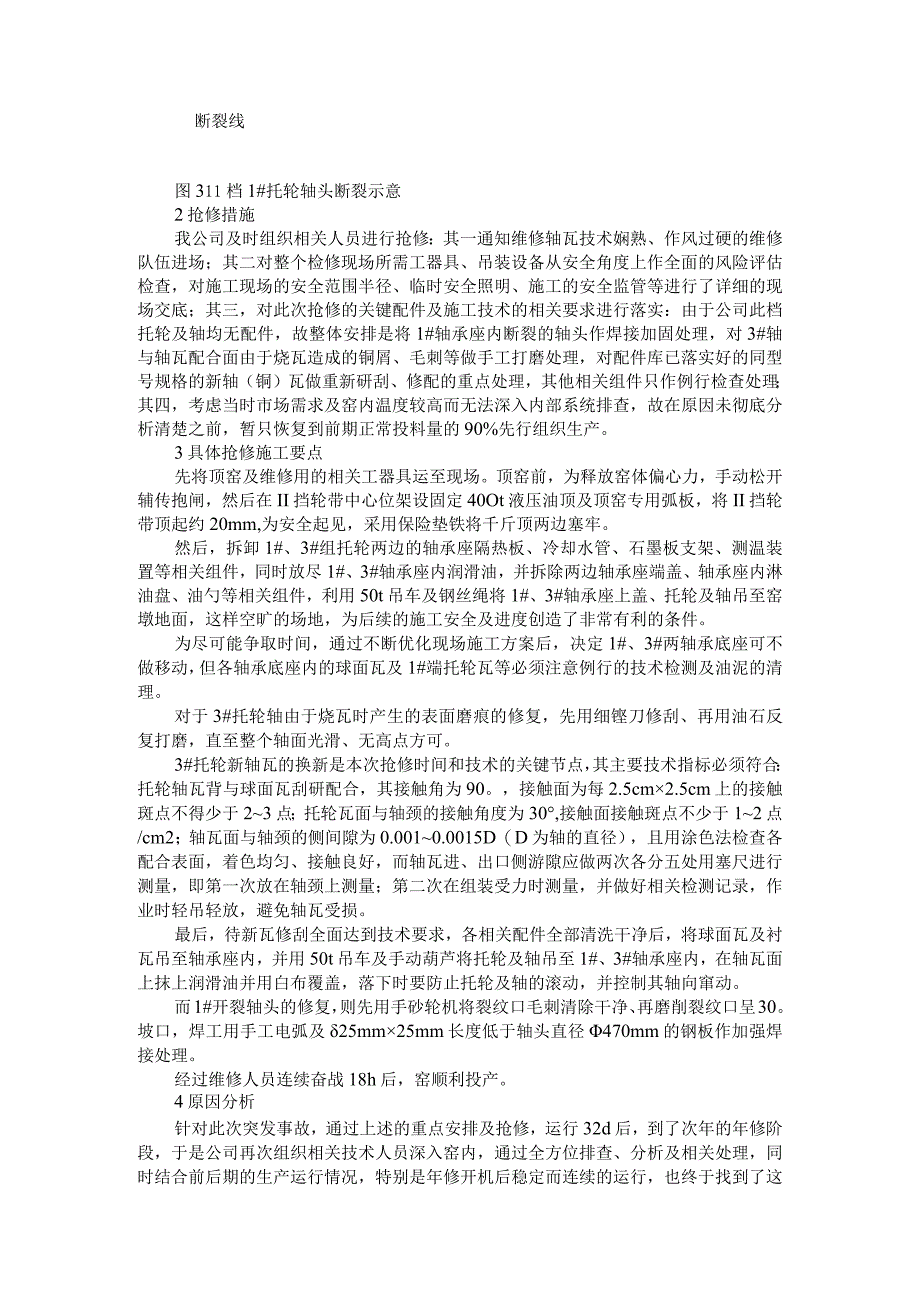
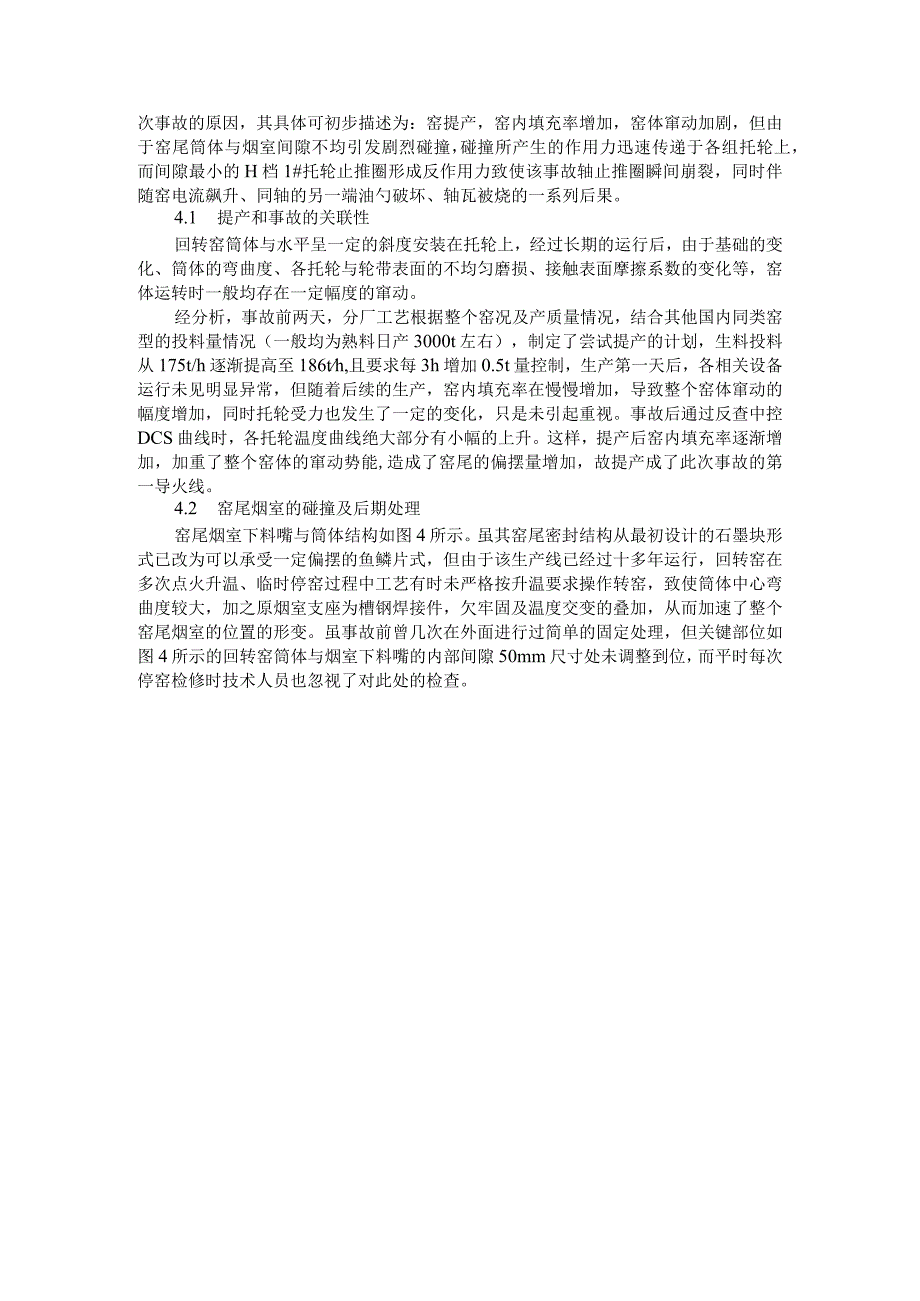
- 配套讲稿:
如PPT文件的首页显示word图标,表示该PPT已包含配套word讲稿。双击word图标可打开word文档。
- 特殊限制:
部分文档作品中含有的国旗、国徽等图片,仅作为作品整体效果示例展示,禁止商用。设计者仅对作品中独创性部分享有著作权。
- 关 键 词:
- 2500t d回转窑托轮轴瓦事故的处理及实例分析 2500 回转 托轮 轴瓦 事故 处理 实例 分析
