稳定层混合料质量通病防治措施.docx
《稳定层混合料质量通病防治措施.docx》由会员分享,可在线阅读,更多相关《稳定层混合料质量通病防治措施.docx(6页珍藏版)》请在第壹文秘上搜索。
1、稳定层混合料质量通病防治措施1、混合料配合比不稳定(1)现象:混合料的水灰比及含水量变化大,其偏差常超出允许范围。混合料的色泽不一,含水量多变。在现场碾压23遍后,出现表面粗糙,石料露骨或过分光滑。现场取样的试件强度离散大。(2)原因分析:采石厂供应的碎石级配不准确,料源不稳定;料堆不同部位的碎石由于离析而粗细分布不均、影响了配比、外观及强度。拌和场混合料配合比控制不准,含水量变化对重量影响未正确估算;计量系统不准确或仅凭经验按体积比放料,甚至连续进料和出料,使混合料配合比波动。混合料放到堆场时,由于落差太高造成离析;出厂又末翻拌,加剧了配合比变化。现场摊铺时,由于人工或机械原因造成粗细分离。
2、(3)预防措施:骨料级配必须满足设计要求,采购时应按规定采购,进料时进行抽检,符合要求后使用。混合料拌和场,必须配备计量斗,对各种原材料按规定的重量比计量;要求不高时也可按材料松容重折算成体积比,进行计量控制。每种原材料的数量应控制在其使用量的5%误差范围内。当含水量变化时,要随时调整计量,或调整体积比保证进料比准确。混合料拌制时,拌和机应具备联锁装置,即进料门和出料门不能同时开启,以防连续出料,造成配合比失控。堆场混合料有离析时,在出厂前必须用装载机(铲车行翻堆,使堆料上下翻拌均匀。装车时铲斗不要过高,以免混合料离析。加强混合料配比抽检,凡超出质量标准范围,必须重新拌制,达到质量要求后才能出
3、场。(4)治理方法:发现现场的混合料粗细料分离,应在现场重新翻拌均匀后再摊铺或者退料。局部范围出现露骨、或过分光滑,可局部翻松IOcm厚度以上,撒入预拌好的混合料抖匀后,再重新碾压。掺加量视具体情况而定。2、混合料含水量波动大(1)现象:送至工地的混合料含水量不均匀,忽高忽低,无法正常摊铺、碾压,给施工时的放样,松铺系数的确定,摊铺、碾压带来困难,影响设计标高、平整度、压实度的有效控制。(2)原因分析:混合料拌制时,加水过多。混合料堆置时间过长而造成混合料过干。混合料出厂时,未经翻堆而造成含水量不均匀。(3)预防措施:混合料的出厂含水量应控制在混合料的最佳含水量上浮25%的范围内,根据天气清况
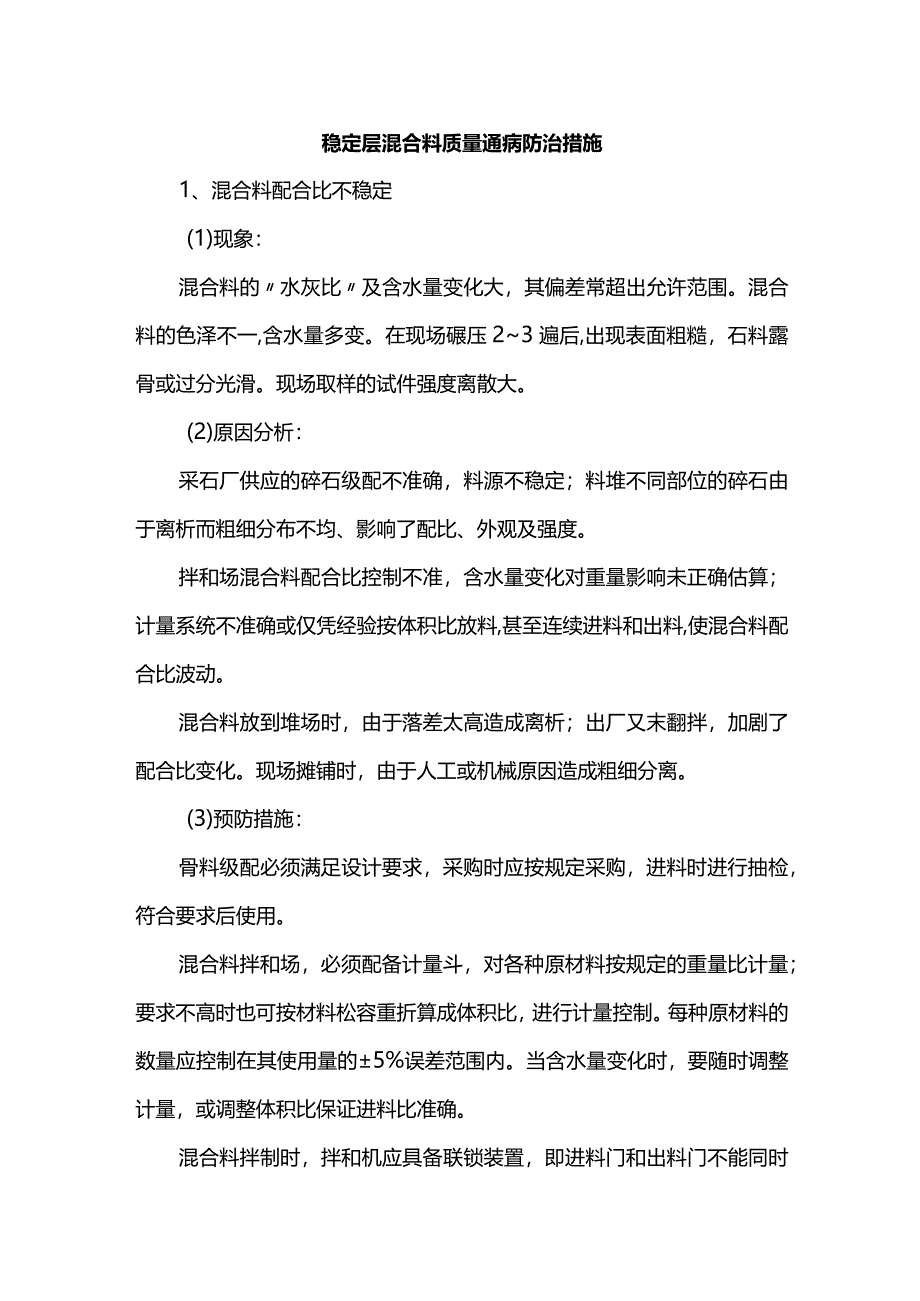

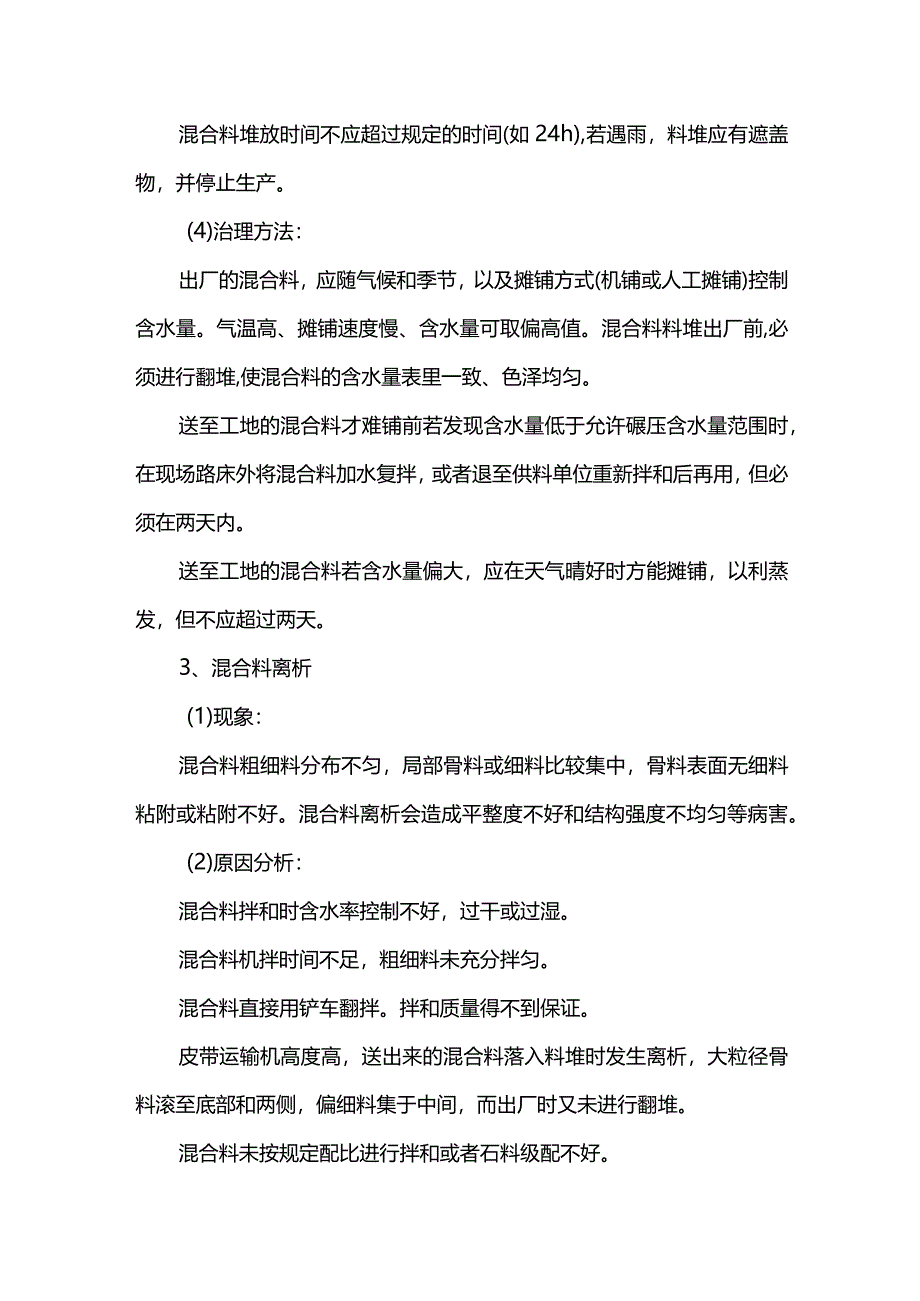
- 配套讲稿:
如PPT文件的首页显示word图标,表示该PPT已包含配套word讲稿。双击word图标可打开word文档。
- 特殊限制:
部分文档作品中含有的国旗、国徽等图片,仅作为作品整体效果示例展示,禁止商用。设计者仅对作品中独创性部分享有著作权。
- 关 键 词:
- 稳定 混合 质量 通病 防治 措施
